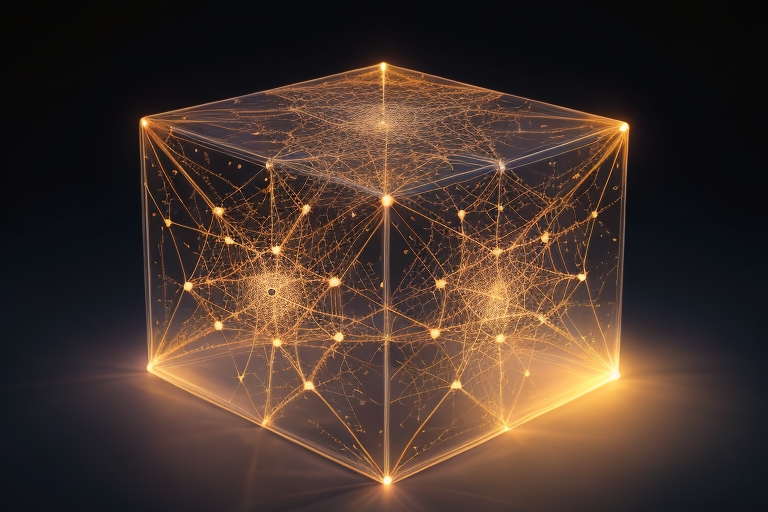
- August 15, 2023
- allix
- Research
A novel approach has revolutionized the intricate materials construction process by introducing an innovative interface, empowering researchers to swiftly conceptualize a plethora of cellular metamaterial configurations, each possessing distinct mechanical attributes.
Engineers persistently seek materials that embody innovative and desirable combinations of properties. For instance, the creation of an exceptionally robust yet lightweight substance could revolutionize the fuel efficiency of airplanes and automobiles, while materials featuring both porosity and biomechanical compatibility could find utility in the realm of bone implants.
Cellular metamaterials, artificial structures characterized by repetitive patterns of constituent units or cells, emerge as promising solutions for achieving these ambitious goals. Nonetheless, pinpointing the specific cellular composition that yields desired attributes remains a formidable challenge. Even when focusing on structures composed of modular elements like interconnected beams or delicate plates, the multitude of potential arrangements is virtually limitless.
Researchers hailing from the Massachusetts Institute of Technology (MIT) and the Institute of Science and Technology Austria (ISTA) have engineered a computational methodology designed to streamline the process of designing metamaterial cells using various modular units and promptly evaluating the resulting material’s characteristics.
Resembling a specialized computer-aided design (CAD) system tailored for metamaterials, this novel approach empowers engineers to rapidly model intricate metamaterials, including those with formidable complexity, expediting the development process that would otherwise span days. The user-friendly interface facilitates comprehensive exploration of the vast array of potential metamaterial shapes, capitalizing on the entire spectrum of available building blocks.
Liane Makatura, an electrical engineering and computer science graduate student at MIT and co-lead author of the study, elaborates, “We devised a representation that encompasses all the diverse shapes engineers have historically demonstrated interest in. Since they can all be constructed using the same methodology, transitioning between them becomes remarkably fluid.”
The paper detailing this breakthrough was co-authored by Makatura alongside Bohan Wang, an MIT postdoctoral researcher; Yi-Lu Chen, a graduate student at ISTA; Bolei Deng, an MIT postdoc; Chris Wojtan and Bernd Bickel, ISTA professors; and senior author Wojciech Matusik, a professor of electrical engineering and computer science at MIT, who spearheads the Computational Design and Fabrication Group within the MIT Computer Science and Artificial Intelligence Laboratory. The culmination of their research will be presented at SIGGRAPH.
A Unified Paradigm
When a scientist endeavors to create a cellular metamaterial, they commence by selecting a representation that will serve as the foundation for their potential designs. This choice fundamentally dictates the spectrum of shapes available for exploration.
For instance, an engineer might opt for a methodology that employs interconnected beams to represent metamaterials. However, this approach constrains the exploration of alternative designs based on different components, such as delicate plates or intricate 3D configurations like spheres. These distinctive shapes are governed by disparate representations, and until now, no comprehensive framework has united all these forms under a single methodology.
Makatura and her team adopted a holistic perspective, meticulously examining an array of metamaterials. They observed that the shapes constituting the overall structure could be efficiently expressed in terms of lower-dimensional forms—an interconnected beam could be distilled to a linear element, and a thin shell could be compressed into a flat surface.
The researchers identified a recurring pattern of symmetry within cellular metamaterials, enabling a significant portion of the structure to be represented succinctly. The remaining portion could be generated through the application of rotations and reflections on the initial fragment.
Guided by these insights, they arrived at the notion that cellular metamaterials could be aptly depicted using a graph-based structure. In their representation, users construct a metamaterial framework by assembling building blocks that manifest as vertices and edges. To illustrate, constructing a beam configuration involves placing a vertex at each terminus of the beam and connecting them through a line segment.
Subsequently, users can manipulate a function along this line segment to determine the thickness of the beam, allowing for variations where distinct segments possess differing thicknesses.
Analogous principles apply to surface structures—a user identifies vital features by marking vertices and then selects a solver to deduce the remaining aspects of the surface.
These solvers, designed for user-friendliness, expedite the construction of even the most intricate metamaterial types, including the complex triply periodic minimal surfaces (TPMS). While potent, conventional TPMS development processes are arduous and prone to setbacks.
“With our approach, users can also begin to amalgamate these shapes. For instance, a unit cell that encompasses both a TPMS structure and a beam structure might yield intriguing properties. Yet, to date, such combinations have remained largely unexplored,” Makatura reveals.
Upon finalization, the system generates an encompassing graph-based blueprint, detailing each step undertaken by the user to achieve the ultimate structure. This comprehensive representation encompasses vertices, edges, solvers, transformations, and thickening operations.
The interface provides designers with the opportunity to preview the evolving structure at any juncture of the construction process, thereby enabling real-time assessment of certain attributes like stiffness. Iterative fine-tuning of parameters facilitates the pursuit of an ideal design.
User-Centric Innovation
The researchers leveraged their system to recreate an array of structures spanning diverse metamaterial classifications. Once the skeletal frameworks were established, generating each metamaterial structure necessitated mere seconds.
Automated exploration algorithms were also devised, each equipped with predefined rules before being set loose within the system. In a test scenario, an algorithm yielded over a thousand potential truss-based structures within an hour.
The researchers conducted a user study involving individuals with minimal prior experience in metamaterial modeling. These participants successfully modeled all six provided structures, with most concurring that the procedural graph representation greatly streamlined the process.
“Our representation renders an array of structures accessible to individuals. We were particularly gratified by the participant’s ability to generate TPMS structures. Even for experts, these intricate designs have historically posed challenges. Remarkably, one TPMS structure featured the shortest average modeling time among all six structures, a revelation that is both surprising and exhilarating,” Makatura shares.
The researchers aspire to enhance their methodology by incorporating more intricate skeleton thickening procedures, broadening the scope of modelable shapes. Moreover, they plan to delve deeper into the utilization of automatic generation algorithms.
Ultimately, their long-term vision entails employing this system for inverse design, wherein desired material properties are specified, and an algorithm identifies the optimal metamaterial structure.
Funding for this research stems from various sources, including a National Science Foundation Graduate Research Fellowship, the MIT Morningside Academy Design Fellowship, the Defense Advanced Research Projects Agency (DARPA), an ERC Consolidator Grant, and the NewSat project.
Categories
- AI Education (39)
- AI in Business (65)
- AI Projects (87)
- Research (77)
- Uncategorized (3)
Other posts
- Neck Liposuction Abroad: Say Goodbye to Double Chin, Hello to Defined Confidence
- Dental Veneers Abroad: Get Your Dream Smile for Less
- Endoscopic Brain Surgery Abroad: Safe, Affordable & Advanced Options You Can Trust
- Say Goodbye to Unwanted Moles: Discover Safe, Affordable Mole Removal Abroad
- Mastoidectomy Abroad: Affordable, Safe, and Life-Changing Ear Surgery
- Buccal Fat Extraction: Sculpt Your Dream Look with the Experts at Best Clinic Abroad
- Get Fast Relief from Spinal Fractures: Kyphoplasty Surgery Abroad with BestClinicAbroad
- Curious About Genetic Testing for Fertility? Here’s What You Need to Know (and Why People Trust Best Clinic Abroad to Book It)
- Hip Pain Ruining Your Life? Here’s Why More People Are Getting Hip Replacements Abroad with Best Clinic Abroad
- Breathe Easier: Why Best Clinic Abroad is Your Top Choice for Septoplasty
Newsletter
Get regular updates on data science, artificial intelligence, machine