Scientists have Pioneered a Novel Soft and Scalable Robotic Hand
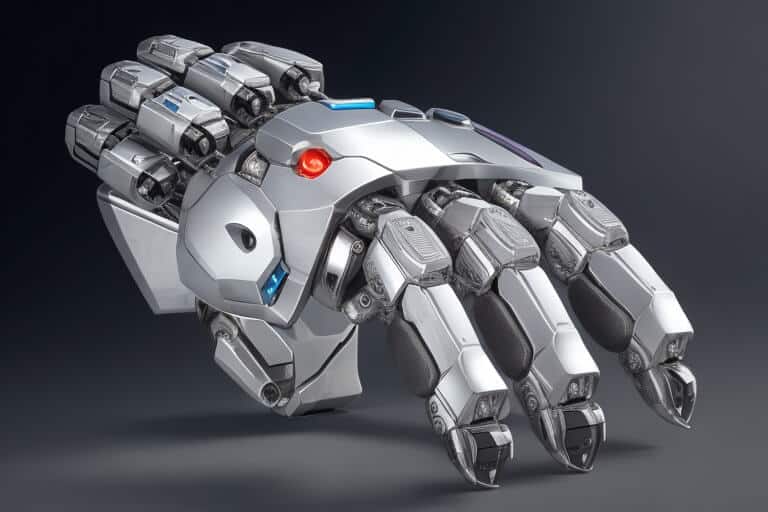
- September 4, 2023
- allix
- AI Projects
Traditional robots are typically constructed from rigid materials, yet nature’s soft-bodied organisms suggest a promising avenue for innovation. The team at the University of Coimbra in Portugal has unveiled an innovative soft robotic hand that boasts affordability and streamlined fabrication techniques. Their breakthrough design integrates soft actuators with an exoskeleton, both crafted through scalable methods.
Robots are typically constructed using a variety of rigid materials, including metals like aluminum and steel, as well as hard plastics such as polycarbonate. These materials are chosen for their durability, stability, and ability to withstand repetitive mechanical stress. Metals like aluminum are lightweight yet strong, making them suitable for robot frames and structural components. Steel is known for its robustness and resilience, often used in heavy-duty industrial robots. Hard plastics provide insulation, protection, and precision in manufacturing robot parts. The combination of these materials ensures that robots can operate effectively in a wide range of environments and perform tasks that require both strength and precision.
Pedro Neto, a member of the research team, emphasized the significance of this shift, stating, “The majority of robotic structures rely on inflexible materials. Yet, when we study the animal kingdom, we observe a fascinating blend of firm elements (like skeletons) and pliable elements (such as muscles) shaping their bodies. Certain creatures, such as earthworms, possess entirely malleable bodies. Drawing inspiration from this natural diversity, we envision the forthcoming era of robots to integrate elements crafted from supple materials, and in some instances, they may even embrace full soft-bodied designs.”
In comparison to their rigid counterparts, soft robotic systems offer enhanced safety and compatibility with humans and animals in various environments, be it outdoors or indoors. These robots pose a reduced risk of causing significant harm or injuries when colliding with humans, animals, or objects in their surroundings.
Neto and his colleagues set out to create a soft robotic hand that is both cost-effective and secure, facilitating large-scale deployment and driving progress in the realm of robotics. Employing finite element analysis for design optimization, they managed to cut prototyping costs before physically crafting the hand. Regular 3D printing was instrumental, allowing them to print components in soft materials and molds in rigid materials.
The resulting soft robotic hand comprises a blend of materials, meticulously designed to mimic the appearance and functionality of human hands, replicating their movements and capabilities. Neto provided insight into the design of the robotic hand, highlighting its unique structure. The hand comprises five soft actuators, each aligned with a finger, and an exoskeletal framework to enhance the flexibility of the fingers. A dedicated ON-OFF controller precisely manages the finger bending angles, allowing the hand to adeptly grasp objects of diverse shapes, weights, and dimensions.
The researchers conducted extensive simulations and experiments to evaluate the performance of their creation. Their preliminary findings are highly promising, as the robotic hand adeptly grasped objects of diverse shapes, weights, and sizes.
Neto highlighted the primary achievement: “The integrated design-fabrication system that utilizes finite element analysis to optimize the design prior to their fabrication.” This innovation holds the potential to enhance the accessibility of soft robotic hands, lowering costs and expediting design-fabrication processes that typically rely on resource-intensive iterative workflows.
Looking ahead, this soft robotic hand could serve as a valuable tool for academic researchers and individual roboticists to experiment with new artificial intelligence (AI) algorithms and computational tools aimed at advancing robot capabilities. Moreover, its design could pave the way for cost-effective humanoid robots designed to assist with various everyday tasks.
Neto further elaborated on our forthcoming research endeavors, emphasizing our commitment to advancing the production of soft actuators and sensors. This endeavor seeks to expand the accessibility of soft robots to a more extensive user base. Additionally, we are actively exploring the realm of controlling soft robots through artificial intelligence, opening up yet another promising avenue of inquiry.
Categories
- AI Education (39)
- AI in Business (65)
- AI Projects (87)
- Research (77)
- Uncategorized (3)
Other posts
- Neck Liposuction Abroad: Say Goodbye to Double Chin, Hello to Defined Confidence
- Dental Veneers Abroad: Get Your Dream Smile for Less
- Endoscopic Brain Surgery Abroad: Safe, Affordable & Advanced Options You Can Trust
- Say Goodbye to Unwanted Moles: Discover Safe, Affordable Mole Removal Abroad
- Mastoidectomy Abroad: Affordable, Safe, and Life-Changing Ear Surgery
- Buccal Fat Extraction: Sculpt Your Dream Look with the Experts at Best Clinic Abroad
- Get Fast Relief from Spinal Fractures: Kyphoplasty Surgery Abroad with BestClinicAbroad
- Curious About Genetic Testing for Fertility? Here’s What You Need to Know (and Why People Trust Best Clinic Abroad to Book It)
- Hip Pain Ruining Your Life? Here’s Why More People Are Getting Hip Replacements Abroad with Best Clinic Abroad
- Breathe Easier: Why Best Clinic Abroad is Your Top Choice for Septoplasty
Newsletter
Get regular updates on data science, artificial intelligence, machine